以空壓機為代表的動力中心是制造型企業非常重要的組成部分,也是企業能耗管理重點所在。正是因其特殊性和代表性,動力中心的“智能化”升級,已被看作是傳統制造企業擁抱工業互聯網,進行產業升級轉型的第一步和最佳“切入點”。

“智慧氣站”解決方案的核心是基于數字化物聯網技術開發的,集成了通訊、采集、計算、控制、存儲等功能的壓縮空氣全方位管理。有各種控制機柜部署在氣站現場,使用物聯工業網關適配器Aprus采集空壓機的控制器與電能表、管道的計算儀,用氣末端的壓力變送器等設備運行參數,再使用網線、Wifi或4G等方式,把采集到的運行參數上報到部署在控制機柜中的MixIOT平臺,通過MixIOT的動態配載(Dynaload)功能運用科學的算法計算最優空壓機組配載策略,控制空壓機運行狀態。MixIOT對氣站設備狀態進行呈現、監控、統計、存儲、預警,通過大數據分析,對空壓機組優化策略進行更合理的調整和優化。通過路由器將MixIOT平臺處理后的數據上報到云平臺,使用電腦、手機app對智慧氣站進行遠程管理空壓機運行狀態。
某傳感器制造公司項目改造案例
實施前客戶氣站狀況:
主要有4個廠房,每個廠房獨立使用一臺變頻空壓機,一線、二線、三線廠房之間管道是互通的,廠房與廠房之間的管道中間裝有閥門,為常閉狀態。四線廠房完全獨立,因此,四個廠房可以默認為是相互獨立用氣。
空壓機產生壓縮空氣主要用于兩部分:
1、車間生產用氣,提供車間設備用氣,氣壓需保持在0.75MPa左右。2、給制氮機供氣,生產出氮氣供黑料罐和戊烷罐使用,末端氣壓基本只需保持在0.2MPa以上即可。

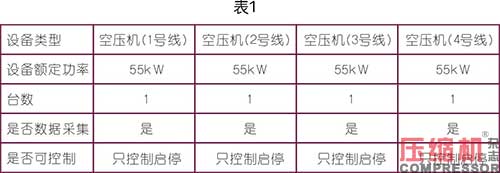

每個車間氣站主要由1臺空壓機+2個儲氣罐+1根生產用氣管道+1根制氮用氣管道組成,具體情況如下:
1、空壓機:4臺,功率:55kW。2、空壓機儲氣罐:4個,容積:2m3。3、氮氣儲氣罐:4個,容積:2m3。4、電能表:4個,一臺空壓機配一個電表。5、用氣末端壓力:分為生產用氣和氮氣,生產用氣直接使用壓縮空氣;氮氣是將壓縮空氣經過制氮機后分離出用于黑料罐和戊烷罐。(1)生產用氣:壓力直接讀取空壓機排氣壓力。(2)氮氣末端:
●一線,直接讀取兩個黑料罐壓力;
●二線,增加壓力變送器,讀取戊烷罐末端壓力。
●三線,直接讀取三個黑料罐壓力,增加壓力變送器,讀取戊烷罐末端壓力。
●四線,增加壓力變送器,讀取黑料罐和戊烷罐共用主管道末端壓力。
使用壓縮空氣的主要生產設備:
1、雙帶機、帶鋸機、碼垛機、涼床,生產時開機,停產時關機。2、戊烷罐、黑料罐,生產時開機,停產時需保證罐內壓力不處于負壓狀態,因此需實時監控進行補充壓縮空氣,接線圖如圖2。
每條線氣站主要耗電設備如表1。
上述空壓機都是變頻空壓機,給各個車間提供生產用氣和氮氣原料輸入,車間不生產時,生產用氣可關閉,但氮氣末端壓力,即使不生產時也需要保證末端壓力正常。因此,車間空壓機需保持24H開啟,用于保證氮氣末端壓力正常,停產狀態下,黑料罐和戊烷罐消耗氮氣極少。車間7:50-19:00屬于上班時間,夜間不生產;并且車間換線時間較長(大約1-2小時),以及白天不生產的情況。這些情況下,一直將空壓機保持開啟狀態存在很大的能耗浪費。因此,實時監控氮氣末端壓力,壓力正常時關閉空壓機,接近異常時,開啟空壓機,對于節能降耗有很大的幫助。
客戶氣站能耗分析如圖3。
圖3為項目實施前一線空壓機10天電量消耗和運行情況,可以很明顯地看出空壓機24小時都處于開機運行狀態,即使夜間停產,為保證黑料罐、戊烷罐壓力正常,空壓機仍然開啟著,并且一直處于加載狀態,每小時大約有33kW·h的電量損耗。另外,從上圖還可以看出,白天生產時也有較多的時間處于換線或者停產狀態,但空壓機也是開啟著,并一直處于加載狀態,造成電量的浪費。根據現場了解到,停產或換線時,基本只需要保證黑料罐、戊烷罐壓力正常即可,生產不需要用氣,而黑料罐和戊烷罐在停產狀態下用氣量極少,只需偶爾補充氮氣罐氣體即可,但因為無法實時把控黑料罐和戊烷罐末端壓力,為保證安全和后續正常生產,所以只能一直將空壓機開啟,保證充足供氣。另外換線或停產狀態下,產線沒有關閉生產用氣閥門的習慣,導致壓縮空氣一直經過生產管道被排放,因此,管道壓力一直無法達到卸載壓力要求,空壓機一直處于加載狀態。
通常情況下,造成氣站有效利用率較低的原因一般分為以下四種:
1、空壓機本身配置參數不匹配原因;
2、設備維護不到位,或維保不及時導致;
3、設備、管道規劃不合理,及管道密封不好,有漏氣現象存在發生;
4、生產現場用氣與氣站機房人員無法實時確認現場用氣,以至供需不平衡導致。
根據現場情況和客觀條件限制,本次項目主要針對第四種原因制定具體解決方案。
針對該客戶的具體方案:
通過上述分析,要優化當前氣站提高利用率,主要需解決一個方面的問題,即供需不平衡導致的浪費問題。增加系統自動控制功能,實時監控每個氣站黑料罐、戊烷罐的末端壓力,當產線停產時,自動關閉空壓機,當監控到黑料罐、戊烷罐的末端壓力接近最低值時,系統自動開啟空壓機,及時補充末端氮氣,保證末端壓力正常。
由此形成的針對該客戶的具體控制策略如表2。
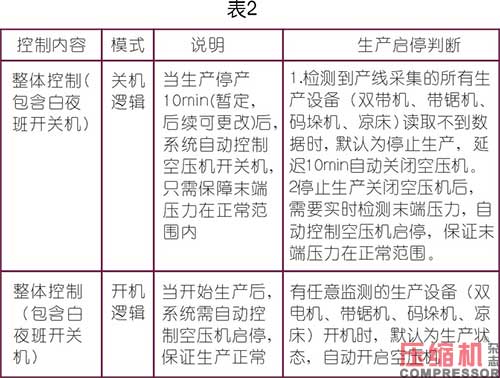
項目實施后節能效果:

圖4是對一線夜間空壓機自動控制后的電量曲線圖。
控制前,空壓機夜間每小時耗電大約33kW·h,控制后,空壓機夜間每小時耗電大約2kW·h左右。大約平均每小時減少30kW·h的耗電。一般夜間停產時間大約為10-12個小時,取平均值11小時。因此,一臺空壓機一晚可節約用電30×11=330kW·h,一臺空壓機一個月僅夜間可節約電量近10000kW·h。
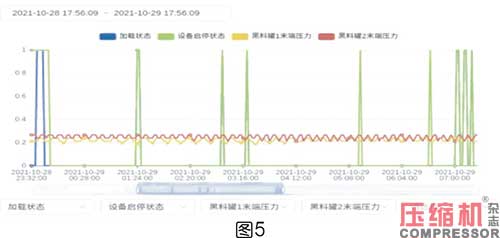
圖5是一線空壓機狀態和氮氣末端壓力曲線圖,系統根據夜間氮氣末端壓力,自動對空壓機進行開關機控制,保證氮氣末端壓力保持在正常范圍。
通過系統的自動控制,大大減少了空壓機的運行時間,有效的保證了氮氣末端壓力的正常,在安全和節能上達到統一。
二、三、四線節能前與一線情況一樣,將自動控制擴展至二、三、四線后,停產狀態下的節能效果也有了較大的提升,解決了空壓機在停產狀態下依舊要持續運行來保證氮氣末端壓力正常的問題,通過實時監測和自動控制,做到了既保證氮氣末端壓力正常,且減少空壓機無效做功的問題。以下為其它三條線節能后的效果曲線圖。



本項目未實施前,每臺空壓機日耗電量大約在1000kW·h,即4臺空壓機月耗電約120000kW·h。項目實施后,每臺空壓機每日大約可節電330kW·h,即4臺空壓機月節電可達40000kW·h,節電率約30%。
來源:本站原創
以空壓機為代表的動力中心是制造型企業非常重要的組成部分,也是企業能耗管理重點所在。正是因其特殊性和代表性,動力中心的“智能化”升級,已被看作是傳統制造企業擁抱工業互聯網,進行產業升級轉型的第一步和最佳“切入點”。
“智慧氣站”解決方案的核心是基于數字化物聯網技術開發的,集成了通訊、采集、計算、控制、存儲等功能的壓縮空氣全方位管理。有各種控制機柜部署在氣站現場,使用物聯工業網關適配器Aprus采集空壓機的控制器與電能表、管道的計算儀,用氣末端的壓力變送器等設備運行參數,再使用網線、Wifi或4G等方式,把采集到的運行參數上報到部署在控制機柜中的MixIOT平臺,通過MixIOT的動態配載(Dynaload)功能運用科學的算法計算最優空壓機組配載策略,控制空壓機運行狀態。MixIOT對氣站設備狀態進行呈現、監控、統計、存儲、預警,通過大數據分析,對空壓機組優化策略進行更合理的調整和優化。通過路由器將MixIOT平臺處理后的數據上報到云平臺,使用電腦、手機app對智慧氣站進行遠程管理空壓機運行狀態。
某傳感器制造公司項目改造案例
實施前客戶氣站狀況:
主要有4個廠房,每個廠房獨立使用一臺變頻空壓機,一線、二線、三線廠房之間管道是互通的,廠房與廠房之間的管道中間裝有閥門,為常閉狀態。四線廠房完全獨立,因此,四個廠房可以默認為是相互獨立用氣。
空壓機產生壓縮空氣主要用于兩部分:
1、車間生產用氣,提供車間設備用氣,氣壓需保持在0.75MPa左右。2、給制氮機供氣,生產出氮氣供黑料罐和戊烷罐使用,末端氣壓基本只需保持在0.2MPa以上即可。
每個車間氣站主要由1臺空壓機+2個儲氣罐+1根生產用氣管道+1根制氮用氣管道組成,具體情況如下:
1、空壓機:4臺,功率:55kW。2、空壓機儲氣罐:4個,容積:2m3。3、氮氣儲氣罐:4個,容積:2m3。4、電能表:4個,一臺空壓機配一個電表。5、用氣末端壓力:分為生產用氣和氮氣,生產用氣直接使用壓縮空氣;氮氣是將壓縮空氣經過制氮機后分離出用于黑料罐和戊烷罐。(1)生產用氣:壓力直接讀取空壓機排氣壓力。(2)氮氣末端:
●一線,直接讀取兩個黑料罐壓力;
●二線,增加壓力變送器,讀取戊烷罐末端壓力。
●三線,直接讀取三個黑料罐壓力,增加壓力變送器,讀取戊烷罐末端壓力。
●四線,增加壓力變送器,讀取黑料罐和戊烷罐共用主管道末端壓力。
使用壓縮空氣的主要生產設備:
1、雙帶機、帶鋸機、碼垛機、涼床,生產時開機,停產時關機。2、戊烷罐、黑料罐,生產時開機,停產時需保證罐內壓力不處于負壓狀態,因此需實時監控進行補充壓縮空氣,接線圖如圖2。
每條線氣站主要耗電設備如表1。
上述空壓機都是變頻空壓機,給各個車間提供生產用氣和氮氣原料輸入,車間不生產時,生產用氣可關閉,但氮氣末端壓力,即使不生產時也需要保證末端壓力正常。因此,車間空壓機需保持24H開啟,用于保證氮氣末端壓力正常,停產狀態下,黑料罐和戊烷罐消耗氮氣極少。車間7:50-19:00屬于上班時間,夜間不生產;并且車間換線時間較長(大約1-2小時),以及白天不生產的情況。這些情況下,一直將空壓機保持開啟狀態存在很大的能耗浪費。因此,實時監控氮氣末端壓力,壓力正常時關閉空壓機,接近異常時,開啟空壓機,對于節能降耗有很大的幫助。
客戶氣站能耗分析如圖3。
圖3為項目實施前一線空壓機10天電量消耗和運行情況,可以很明顯地看出空壓機24小時都處于開機運行狀態,即使夜間停產,為保證黑料罐、戊烷罐壓力正常,空壓機仍然開啟著,并且一直處于加載狀態,每小時大約有33kW·h的電量損耗。另外,從上圖還可以看出,白天生產時也有較多的時間處于換線或者停產狀態,但空壓機也是開啟著,并一直處于加載狀態,造成電量的浪費。根據現場了解到,停產或換線時,基本只需要保證黑料罐、戊烷罐壓力正常即可,生產不需要用氣,而黑料罐和戊烷罐在停產狀態下用氣量極少,只需偶爾補充氮氣罐氣體即可,但因為無法實時把控黑料罐和戊烷罐末端壓力,為保證安全和后續正常生產,所以只能一直將空壓機開啟,保證充足供氣。另外換線或停產狀態下,產線沒有關閉生產用氣閥門的習慣,導致壓縮空氣一直經過生產管道被排放,因此,管道壓力一直無法達到卸載壓力要求,空壓機一直處于加載狀態。
通常情況下,造成氣站有效利用率較低的原因一般分為以下四種:
1、空壓機本身配置參數不匹配原因;
2、設備維護不到位,或維保不及時導致;
3、設備、管道規劃不合理,及管道密封不好,有漏氣現象存在發生;
4、生產現場用氣與氣站機房人員無法實時確認現場用氣,以至供需不平衡導致。
根據現場情況和客觀條件限制,本次項目主要針對第四種原因制定具體解決方案。
針對該客戶的具體方案:
通過上述分析,要優化當前氣站提高利用率,主要需解決一個方面的問題,即供需不平衡導致的浪費問題。增加系統自動控制功能,實時監控每個氣站黑料罐、戊烷罐的末端壓力,當產線停產時,自動關閉空壓機,當監控到黑料罐、戊烷罐的末端壓力接近最低值時,系統自動開啟空壓機,及時補充末端氮氣,保證末端壓力正常。
由此形成的針對該客戶的具體控制策略如表2。
項目實施后節能效果:
圖4是對一線夜間空壓機自動控制后的電量曲線圖。
控制前,空壓機夜間每小時耗電大約33kW·h,控制后,空壓機夜間每小時耗電大約2kW·h左右。大約平均每小時減少30kW·h的耗電。一般夜間停產時間大約為10-12個小時,取平均值11小時。因此,一臺空壓機一晚可節約用電30×11=330kW·h,一臺空壓機一個月僅夜間可節約電量近10000kW·h。
圖5是一線空壓機狀態和氮氣末端壓力曲線圖,系統根據夜間氮氣末端壓力,自動對空壓機進行開關機控制,保證氮氣末端壓力保持在正常范圍。
通過系統的自動控制,大大減少了空壓機的運行時間,有效的保證了氮氣末端壓力的正常,在安全和節能上達到統一。
二、三、四線節能前與一線情況一樣,將自動控制擴展至二、三、四線后,停產狀態下的節能效果也有了較大的提升,解決了空壓機在停產狀態下依舊要持續運行來保證氮氣末端壓力正常的問題,通過實時監測和自動控制,做到了既保證氮氣末端壓力正常,且減少空壓機無效做功的問題。以下為其它三條線節能后的效果曲線圖。
本項目未實施前,每臺空壓機日耗電量大約在1000kW·h,即4臺空壓機月耗電約120000kW·h。項目實施后,每臺空壓機每日大約可節電330kW·h,即4臺空壓機月節電可達40000kW·h,節電率約30%。
來源:本站原創
網友評論
條評論
最新評論