【壓縮機網】顯示屏上準確報告著每臺設備的生產情況和物料狀態,產品質量檢驗結果也一目了然。整個車間干凈整潔,機器繁忙的工作聲有節奏地傳來,其間偶爾出現一兩個工人,在廠房確認設備加工情況……
據悉,該項目大量采用國產核心關鍵裝備,打造出國內首條自主研發的轉子線圈銑孔自動流水線、國內首個定子線圈模塊化柔性生產車間、國內首個定子沖片全自動綠色制造車間,建成國內首個多通道定子線圈一體化數字檢測平臺。截至目前,共形成發明專利21項、實用新型專利14項、軟件著作權4項、企業標準5項。
鐵芯和線圈被譽為發電機的“心臟”。過去,其在發電設備行業一直主要依賴手工作業加部分機械化方式,工序繁多、勞動強度大、質量管控風險高。這樣的模式已難以適應客戶個性化需求所催生的高品質、短周期、低成本需要,改變迫在眉睫。
2016年,東方電機成立了智能制造項目執行聯合體,并邀請兩院院士及中國機械工程學會專家現場指導,編撰了智能制造發展規劃(線圈和沖片專項)。經過反復討論設計,提出 “1個平臺+3個數字化車間+N個智能制造單元”的建設思路。
東方電機智能制造新模式項目總投入超過2.2億元,建設范圍涵蓋線圈分廠、沖剪分廠、發電機分廠等多個生產區域。歷時近4年,最終建成一個協同制造平臺,定子線圈、轉子線圈及定子沖片3個數字化車間,打造數字化試驗、典型件柔性制造、機器人集成應用等多個智能制造單元。
東方電機數字化車間建成后,生產效率提高48%,運營成本降低31.9%,產品研制周期縮短30.7%,產品不良品率降低20%,能源利用率提高57.3%。每年可為企業帶來約1.5億元的直接經濟效益。
“原來定子生產線需要11個操作者,如今自動線只需要兩三個人,生產現場的整潔度也明顯改觀。”東方電機沖剪分廠定子組副組長肖鵬介紹,自動生產線避免了很多無效工作,生產效率提高了不少;更重要的是的沖片不經過人手,避免了汗漬銹蝕,質量更有保障。
線圈分廠生產安全組副組長廖汝才表示,自動生產線打破了過去水火電分開的資源組織架構,達到大小定子線圈產品混線生產、水火互補、柔性制造的目的,原來13個生產班組已經優化到7個。“數字化質量檢測能夠實現智能判定從而有效防止誤操作,讓線圈質量得到顯著提升。”
據悉,在智能制造領域,東方電機正醞釀制訂數字化工廠建設2020—2025規劃,打造AI、5G及區塊鏈應用場景,向核心部套裝配、大件加工等領域拓展,開展智能工廠的駕駛艙 (數字中心)研究。
來源:今日電機 四川在線
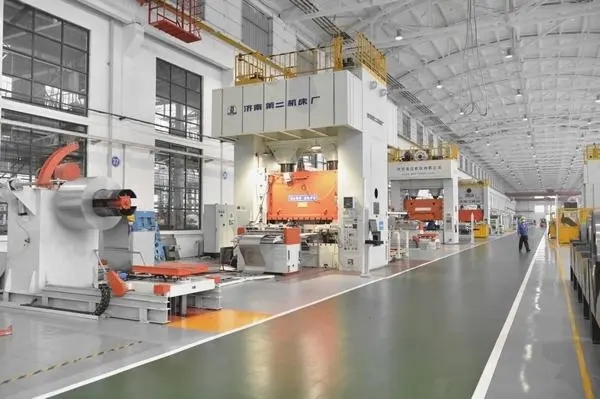
據悉,該項目大量采用國產核心關鍵裝備,打造出國內首條自主研發的轉子線圈銑孔自動流水線、國內首個定子線圈模塊化柔性生產車間、國內首個定子沖片全自動綠色制造車間,建成國內首個多通道定子線圈一體化數字檢測平臺。截至目前,共形成發明專利21項、實用新型專利14項、軟件著作權4項、企業標準5項。
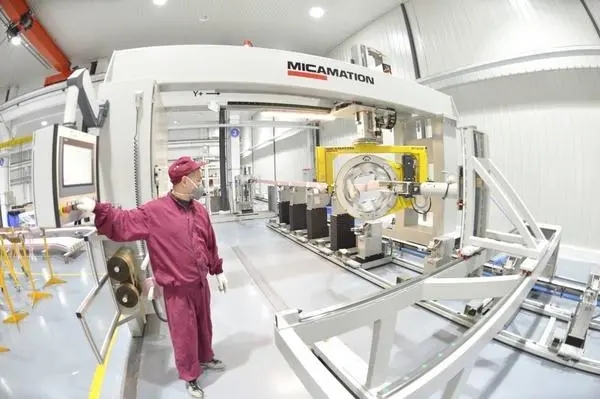
鐵芯和線圈被譽為發電機的“心臟”。過去,其在發電設備行業一直主要依賴手工作業加部分機械化方式,工序繁多、勞動強度大、質量管控風險高。這樣的模式已難以適應客戶個性化需求所催生的高品質、短周期、低成本需要,改變迫在眉睫。
2016年,東方電機成立了智能制造項目執行聯合體,并邀請兩院院士及中國機械工程學會專家現場指導,編撰了智能制造發展規劃(線圈和沖片專項)。經過反復討論設計,提出 “1個平臺+3個數字化車間+N個智能制造單元”的建設思路。
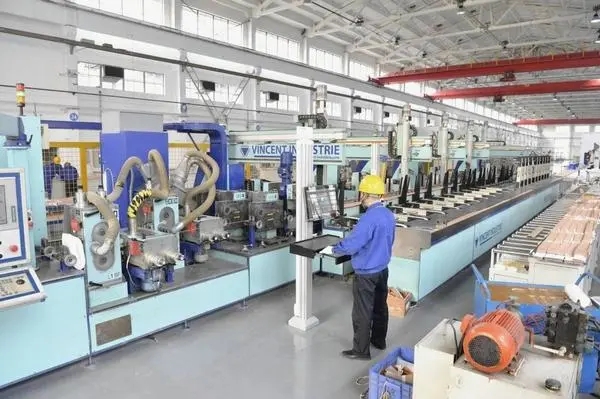
東方電機智能制造新模式項目總投入超過2.2億元,建設范圍涵蓋線圈分廠、沖剪分廠、發電機分廠等多個生產區域。歷時近4年,最終建成一個協同制造平臺,定子線圈、轉子線圈及定子沖片3個數字化車間,打造數字化試驗、典型件柔性制造、機器人集成應用等多個智能制造單元。
東方電機數字化車間建成后,生產效率提高48%,運營成本降低31.9%,產品研制周期縮短30.7%,產品不良品率降低20%,能源利用率提高57.3%。每年可為企業帶來約1.5億元的直接經濟效益。
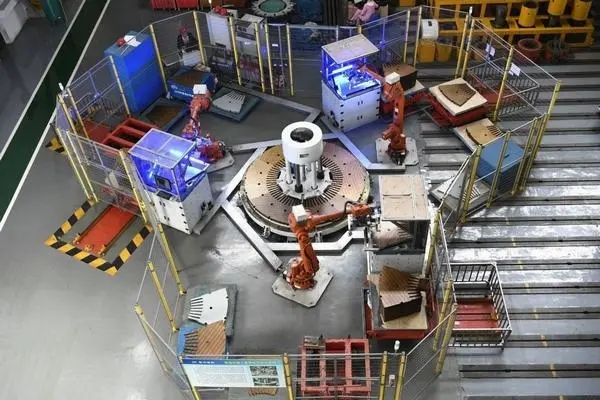
“原來定子生產線需要11個操作者,如今自動線只需要兩三個人,生產現場的整潔度也明顯改觀。”東方電機沖剪分廠定子組副組長肖鵬介紹,自動生產線避免了很多無效工作,生產效率提高了不少;更重要的是的沖片不經過人手,避免了汗漬銹蝕,質量更有保障。
線圈分廠生產安全組副組長廖汝才表示,自動生產線打破了過去水火電分開的資源組織架構,達到大小定子線圈產品混線生產、水火互補、柔性制造的目的,原來13個生產班組已經優化到7個。“數字化質量檢測能夠實現智能判定從而有效防止誤操作,讓線圈質量得到顯著提升。”
據悉,在智能制造領域,東方電機正醞釀制訂數字化工廠建設2020—2025規劃,打造AI、5G及區塊鏈應用場景,向核心部套裝配、大件加工等領域拓展,開展智能工廠的駕駛艙 (數字中心)研究。
來源:今日電機 四川在線
網友評論
條評論
最新評論